Electro Permanent Magnetic Chuck For Workholding
- Constant & uniform clamping and full support of workpiece
- Unlike mechanical clamps and vises, no vibration or chatter
- Allow access to multi-side machining of a workpiece – no need to stop and re-position
- Improved safety – electro permanent magnetic technology guarantees a secure and stable hold of the workpiece even in a power outage
Magnetic Chuck
Electro permanent magnetic chuck for workholding offers secure and efficient clamping for milling, turning, and grinding operations, enhancing productivity and precision.
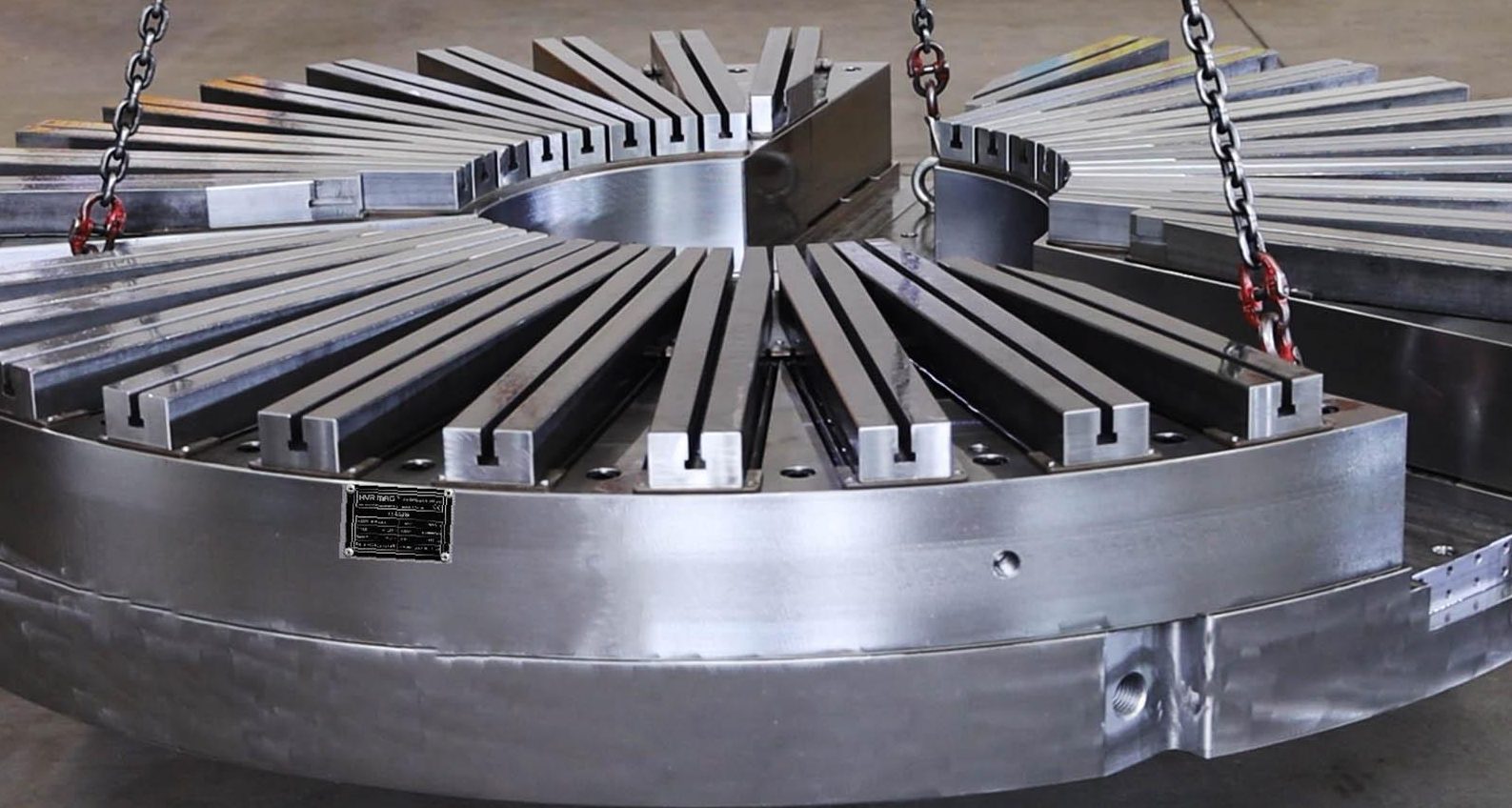
What is Electro Permanent Magnetic Chuck?
An Electro Permanent Magnetic Chuck is a tool made from permanent magnetic materials that utilizes electrical pulses to alter the magnetic field state. It is primarily used for clamping and fixing jobs in various manufacturing, processing, and inspection fields.
The core technology of an electro permanent magnetic chuck is its ability to instantaneously change the polarity of the magnetic field by controlling external current pulses, enabling rapid opening and closing of the chuck, thereby significantly enhancing work efficiency and operational convenience. It is particularly advantageous in situations requiring frequent clamping and releasing of workpieces, especially in processes needing high-precision positioning and high load capacity.
Feature Box of Electro Permanent Magnetic Chuck
Electro permanent magnetic chucks for workholding offer secure and efficient clamping for milling, turning, and grinding operations, enhancing productivity and precision.

Variable power allows all types and sizes of ferrous work pieces to be held.

Perfect safety in case of power failure.

95% energy saving,needs electricity for only 3 seconds during the MAG and DEMAG phase.

2 seconds to activate or deactivate magnetism,5-side machining in one clamp with high accuracy. /Minimum set-up time and increase of productivity.

Modular, Rigid and Robust construction.

No moving parts,100% waterproof all steel surface,increase in tool life and cause no damage to the loads.
Working Principle of Electro Permanent Magnetic Chuck
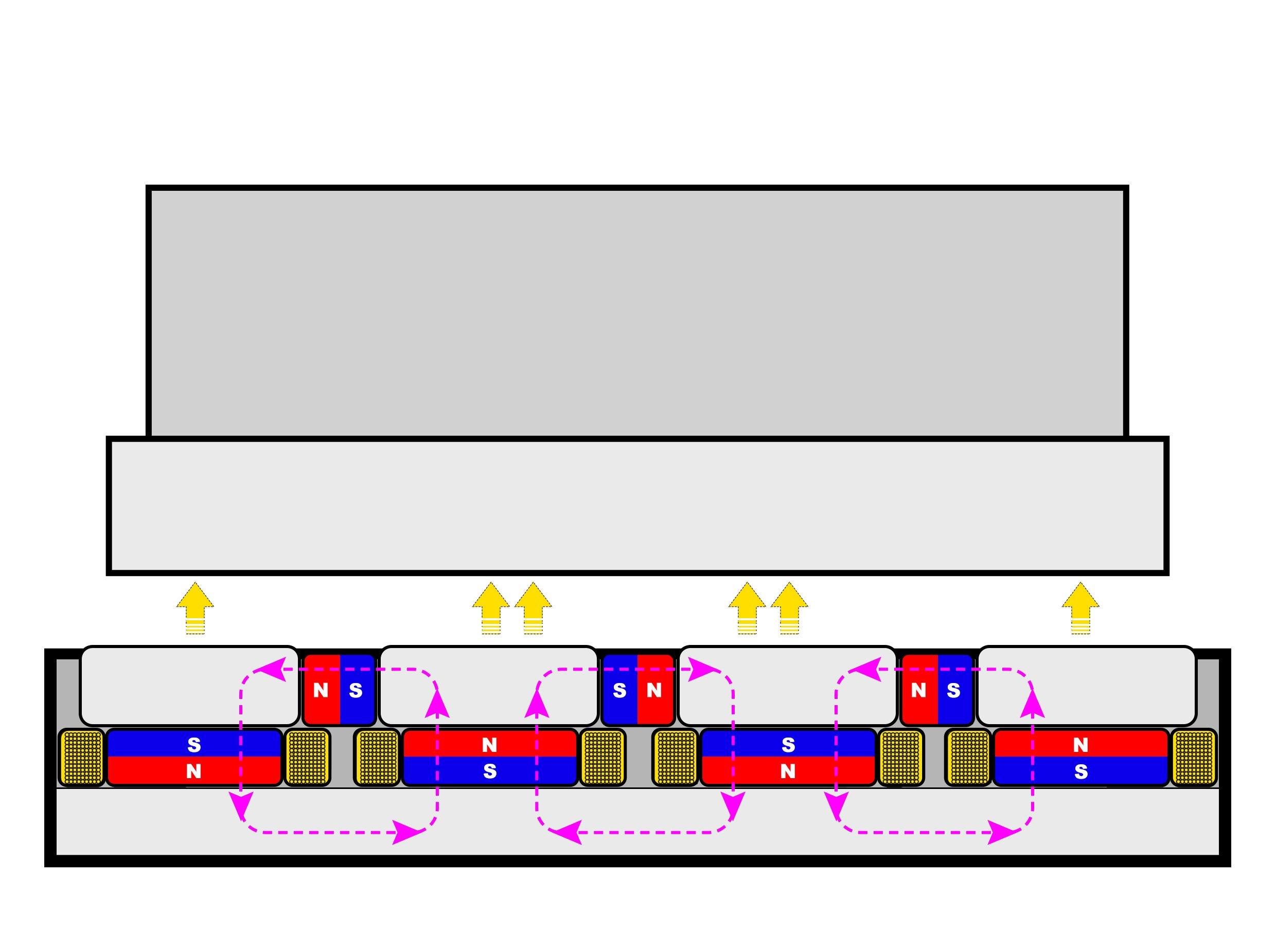
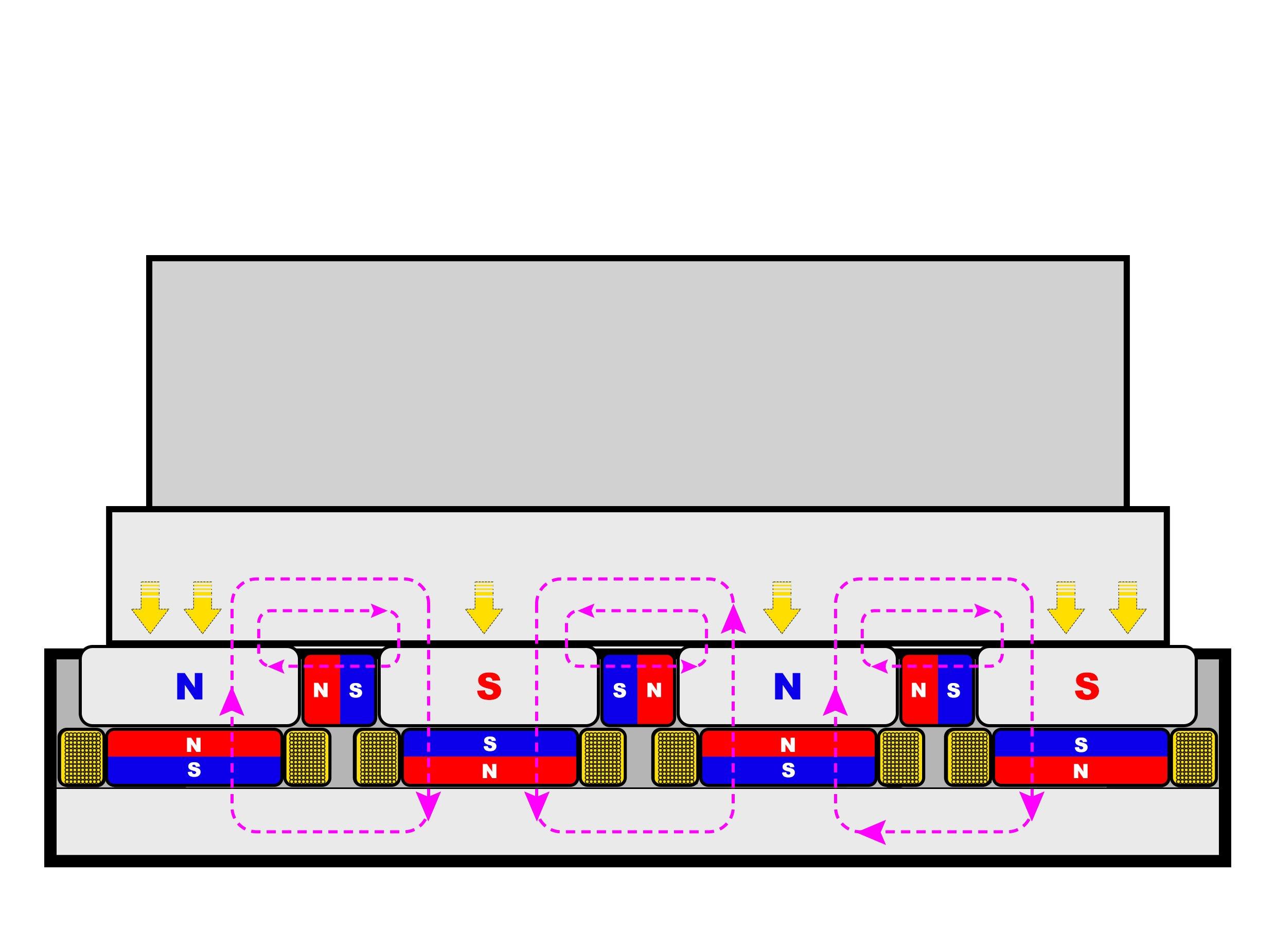
The electro-permanent magnetic chuck combines the characteristics of permanent magnets and electromagnets. It is mainly composed of permanent magnets and electromagnetic coils. In the unpowered state, the magnetic force of the permanent magnet enables the chuck to have a certain suction force and can hold the workpiece.
When it is necessary to clamp or release the workpiece, the electromagnetic coil is energized. When energized, the magnetic field generated by the electromagnetic coil interacts with the magnetic field of the permanent magnet. By controlling the direction and magnitude of the current, the direction and intensity of the electromagnetic field can be changed.
For example, when the current direction makes the electromagnetic field in the same direction as the magnetic field of the permanent magnet, the magnetic force of the chuck is enhanced to achieve the function of clamping the workpiece. And when the current direction makes the electromagnetic field opposite to the magnetic field of the permanent magnet, the two cancel each other out, the magnetic force weakens, and thus the workpiece is released. This working principle makes the electro-permanent magnetic chuck have the advantages of strong magnetic force, energy saving, and convenient operation, etc. It has been widely used in fields such as mechanical processing.
Traditional Chuck vs Electro Permanent Magnetic Chuck
Features | Mechanical Clamps | Permanent Magnetic Chuck | Eletromangetic Chuck | Eletro Permanent Magnetic Chuck |
Magnetic Strength | — | Unable to adjust | The magnetic strength cannot be adjusted in zones. | Adjustable in zones, possibility of automated use with the operation from a control unit. |
Energy Consumption | — | No energy consumption. | Need of a constant power supply with a backup power supply for safety reasons. | Energy saving: EPMs chuck requires power just for magnetization and demagnetization. |
Machining Accuracy | Vibration or chatter leads to low accuracy. | Poor. | Constant power produces heat that can cause distortion of the parts, affecting the functioning and accuracy of the machine. | No heat generation with less threat to machine accuracy. Total magnetic surface used for clamping giving better machining accuracy as reducing chattering. |
Operational Efficiency | Low efficiency and easy deformation. | The mechanical switching system is comparatively less efficient for automated work. | It’s ok. | High efficiency: it gives full access to the five sides of a mold that makes it the ideal choice for multi-side machining. |
Safety | Labor unfriendly. | __ | More chances of accidents because of a power failure that can release any part. | Minimum consumption of electricity with a greater safety factor since the power loss will not result in the release of the part from the chuck. |
Chuck Life | Possibility of wear and tear of the material affects service life. | Possibility of wear and tear of the internal moving parts and magnets, responsible for shortening the life of the permanent chuck. | Without any moving parts inside for less internal wear and tear. | Does not have any moving part inside, with no internal wear and tear,long chuck life and no maintenance needed. |
Work-piece Size | Not flexible. | In-adaptability of chuck dimension and likely less suitable for big and heavy workpieces. | Various dimensions can be produced for the chuck, allowing the user to meet specific requirements of the workpiece size. | Can hold all type and size of ferrous work pieces. |
Temperature | — | Due to the nature of the magnet, it is not suitable for processing parts with a temperature higher than 80°C. | The temperature can be up to 250°C, but heat generation often leads to poor accuracy. | An electro-permanent magnet can withstand high temperatures, the maximum temperature to 180°C. |
Yes, our specially designed floating magnetic blocks help compensate for uneven workpiece surfaces and can prevent deformation.
Yes, as long as the chuck’s rated maximum holding force is sufficient, larger workpieces can be securely held.
Theoretically, up to 16 kg/cm².
For low- to medium-carbon steel, residual magnetism is minimal. High-carbon steel may retain some. We can add a demagnetization feature if needed.
Our chucks use 50×50 mm or 70×70 mm poles with magnetic penetration depths of 13 mm and 18 mm, respectively. If your workpiece thickness exceeds this, the tools won’t be affected. Even below these depths, the magnetic field is weak and unlikely to magnetize tools. Only in very thin or special cases might chip evacuation become an issue.
Yes, we offer custom solutions. Just provide detailed drawings of the contact surface, and we’ll design a chuck tailored to your workpiece and application.